Given the increase in demand accompanying population growth and people’s desires for more convenient lifestyles, there are concerns that, if nothing changes, the demand for raw materials will exceed the Earth’s capacity. Avoiding this will require constructing systems to decouple the environmental footprint caused by growing demand. To succeed in decoupling, Bridgestone is taking steps to improve our resource productivity.
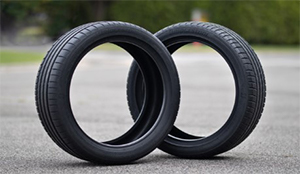
ENLITEN is a technology that evolves environmental performance while expanding basic performance and elevating all conventional performances. It also pursues "ultimate customization" to sharpen the edge in performance which not only meets the apparent needs and potential wants of the markets and customers, but also further inspires markets and customers by creating new value that they may not have imagined, according to the characteristics of diverse vehicles and usage conditions.
With ENLITEN, Bridgestone is expanding products which provide long-life by improving wear resistance performance on top of improving diverse performance desired of tires.
For more information, see “ENLITEN” in Reduce CO2 Emissions .