The Bridgestone Group is committed to continually working toward a more sustainable society to realize long-term environmental, social, and economic benefits across our entire supply chain. Since the initial release of our first Global Sustainable Procurement Policy in 2018, it has built upon its strong foundation and released the third version in 2024. The policy serves as a communication and improvement tool for responsible and sustainable business conduct.
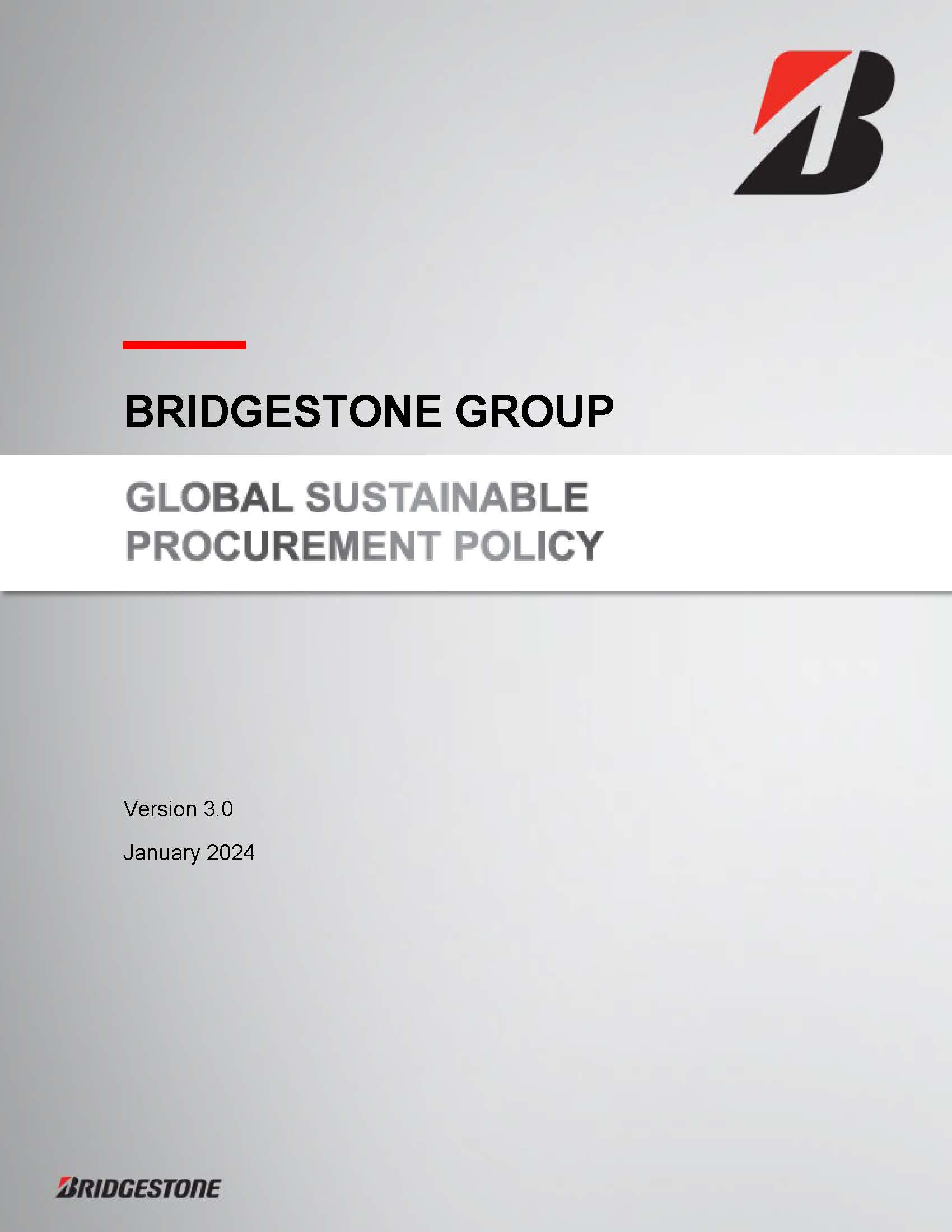